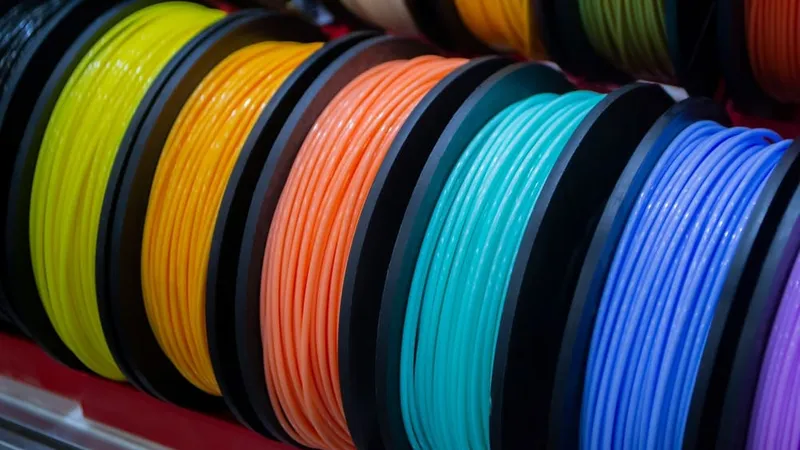
FDM Technology Materials
PLA (Polylactic Acid)
PLA, or Polylactic Acid, is a popular 3D printing material derived from renewable plant-based resources like corn starch and sugarcane. It stands out for its eco-friendliness and ease of use, making it ideal for beginners and educational purposes. PLA is known for its good surface finish and the ability to print at lower temperatures, reducing the risk of warping. However, it lacks the durability and heat resistance required for functional parts in demanding environments, making it better suited for prototypes, toys, and household items.
ABS (Acrylonitrile Butadiene Styrene)
ABS is a strong, heat-resistant thermoplastic commonly used in FDM 3D printing for industrial and functional parts. Its excellent mechanical properties make it suitable for producing robust prototypes, automotive components, and consumer goods. ABS requires a higher printing temperature and a heated bed to prevent warping and ensure good adhesion. Its ability to be post-processed, such as being sanded and smoothed using acetone, adds versatility. Despite its benefits, ABS emits fumes during printing, requiring proper ventilation.
PETG (Polyethylene Terephthalate Glycol)
PETG is a glycol-modified version of PET, combining the durability of ABS with the ease of printing of PLA. It is known for its strength, flexibility, and resistance to moisture, chemicals, and impact. PETG prints at moderate temperatures and has excellent layer adhesion, resulting in strong and durable prints. Its transparency makes it suitable for producing clear parts, while its robustness suits mechanical and functional applications. PETG is less prone to warping compared to ABS, making it user-friendly for a variety of projects.
Nylon
Nylon is a durable, flexible, and resilient material used in FDM 3D printing for producing strong, functional parts. Its high tensile strength and resistance to abrasion and impact make it ideal for mechanical components, gears, and tools. Nylon’s ability to absorb moisture requires careful handling and storage, as excess humidity can affect print quality. It prints at high temperatures and often requires a heated bed to prevent warping. Nylon is valued for its balance of flexibility and strength, making it versatile for various industrial applications.
TPE/TPU (Thermoplastic Elastomer/Polyurethane)
TPE and TPU are flexible, rubber-like materials used in FDM 3D printing for creating parts that require elasticity and resilience. TPE is softer and more flexible, while TPU offers a good balance between flexibility and rigidity. These materials are ideal for producing items like phone cases, seals, and gaskets. They print at moderate temperatures and often require a slower print speed to ensure quality. The main challenge with TPE/TPU is ensuring good adhesion to the print bed, as their flexibility can lead to warping and detachment during printing.
PC (Polycarbonate)
Polycarbonate is a high-performance thermoplastic known for its exceptional strength, impact resistance, and heat tolerance. In FDM 3D printing, it is used for producing parts that require durability and toughness, such as functional prototypes, automotive components, and engineering applications. PC prints at high temperatures and usually requires a heated bed and an enclosed print chamber to prevent warping and ensure good layer adhesion. Its ability to withstand high temperatures and maintain structural integrity makes it a preferred choice for demanding applications.
Stereolithography Materials
Resin 8119
Resin 8119 is a versatile stereolithography material known for its balance of strength and flexibility. It is suitable for producing detailed, high-precision parts with excellent surface finish and intricate features. This resin is commonly used in applications requiring dimensional stability and fine detail, such as dental models, figurines, and prototypes. Its properties allow for easy post-processing, including sanding and painting, making it a popular choice for industries that need accurate and aesthetically pleasing components.
Resin 8118H
Resin 8118H is a high-strength, stereolithography resin designed for applications that require durable and tough parts. It offers excellent mechanical properties, including high tensile strength and impact resistance, making it ideal for functional prototypes, mechanical parts, and engineering components. This resin is known for its ability to produce parts with smooth surfaces and fine details, suitable for end-use applications. Its robust characteristics make it a reliable choice for industries such as automotive and aerospace, where performance and durability are critical.
Resin 8228
Resin 8228 is a high-temperature resistant material used in stereolithography for applications that require parts to withstand elevated temperatures. It is particularly suited for producing components that need to maintain dimensional stability and mechanical properties under heat, such as tooling, molds, and high-performance prototypes. Resin 8228 offers excellent surface quality and precision, making it suitable for detailed and complex parts. Its resistance to thermal deformation makes it an ideal choice for demanding industrial and engineering applications.
Resin 8338
Resin 8338 is a flexible stereolithography resin that provides excellent elasticity and resilience. It is designed for applications requiring soft, rubber-like parts, such as seals, gaskets, and ergonomic grips. This resin combines good tear strength with elongation at break, allowing it to produce durable parts that can endure repeated bending and flexing. Resin 8338 offers smooth surfaces and fine detail resolution, making it suitable for producing functional prototypes and parts that require a combination of flexibility and strength.
Grey Resin
Grey Resin is a popular choice for stereolithography due to its ability to produce highly detailed and smooth parts. Its neutral grey color enhances the visibility of fine features and surface textures, making it ideal for visual prototypes, scale models, and artistic applications. Grey Resin is known for its dimensional accuracy and ease of post-processing, including sanding and painting. Its balanced mechanical properties make it versatile for various applications that require detailed and aesthetically pleasing components.
Mammoth Resin
Mammoth Resin is a stereolithography material used for creating large-scale parts with high precision and excellent surface quality. It is designed for applications that require significant size and structural integrity, such as architectural models, large prototypes, and industrial components. Mammoth Resin provides good mechanical strength and durability, ensuring that large prints maintain their form and function. Its ability to produce intricate details and smooth surfaces on a large scale makes it an ideal choice for projects that demand both size and precision.
Transparent Resin
Transparent Resin is a stereolithography material prized for its clarity and ability to produce parts with excellent optical properties. It is used for applications that require see-through components, such as lenses, light covers, and fluidic devices. This resin offers high detail resolution and smooth surfaces, making it ideal for producing aesthetically pleasing and functional transparent parts. Its clarity and ability to transmit light make Transparent Resin a popular choice for projects where optical quality and visual appeal are important.
SLS Materials
Nylon PA12
Nylon PA12 is a widely used material in Selective Laser Sintering (SLS) known for its strength, durability, and chemical resistance. It is ideal for producing functional parts that require toughness and longevity, such as mechanical components, housings, and gears. Nylon PA12 offers excellent dimensional stability and can withstand repeated mechanical stress and environmental exposure. Its fine powder consistency ensures high detail resolution and surface quality, making it suitable for a range of industrial and engineering applications.
Polyamide
Polyamide, commonly referred to as nylon, is a robust and versatile material used in SLS 3D printing. It is valued for its high strength, flexibility, and resistance to abrasion and chemicals, making it suitable for functional prototypes and end-use parts. Polyamide parts exhibit good dimensional accuracy and surface finish, capable of producing complex geometries and detailed features. Its wide range of applications includes automotive parts, medical devices, and consumer goods, where performance and durability are essential.
Alumide
Alumide is a composite material used in SLS that combines polyamide with aluminum particles. This blend results in parts with unique properties, including improved stiffness, thermal conductivity, and metallic appearance. Alumide is ideal for creating prototypes and functional components that require a balance of strength, heat resistance, and aesthetic appeal. Its ability to produce intricate details and lightweight parts makes it suitable for applications in automotive, aerospace, and consumer products where a metallic finish is desirable.
TPU
Thermoplastic Polyurethane (TPU) is a flexible, rubber-like material used in SLS 3D printing for producing parts that require elasticity and durability. TPU is known for its excellent impact resistance, flexibility, and ability to withstand repeated bending and stretching. It is commonly used for creating functional prototypes, footwear, gaskets, and flexible connectors. TPU’s unique combination of softness and strength allows for the production of parts that need to perform under dynamic and demanding conditions.
SLM Materials
Titanium
Titanium is a high-performance metal used in Selective Laser Melting (SLM) for producing lightweight and strong parts with excellent corrosion resistance. It is ideal for applications in aerospace, medical, and automotive industries, where a combination of low weight, high strength, and biocompatibility is crucial. Titanium parts created with SLM exhibit excellent mechanical properties and precise geometries, making them suitable for critical components like implants, aircraft parts, and high-performance machinery.
Aluminum
Aluminum is a versatile metal used in SLM 3D printing for creating lightweight parts with good strength and thermal conductivity. It is widely used in aerospace, automotive, and consumer electronics due to its favorable strength-to-weight ratio and resistance to corrosion. Aluminum parts produced with SLM are known for their precision, fine details, and smooth surfaces, making them ideal for functional prototypes and end-use components that require high performance and reliability.
Stainless Steel
Stainless Steel is a durable and corrosion-resistant material used in SLM 3D printing for producing robust and long-lasting parts. It is commonly employed in applications requiring high strength, wear resistance, and dimensional accuracy, such as tooling, medical devices, and industrial components. Stainless Steel parts created with SLM offer excellent mechanical properties and a high-quality surface finish, suitable for both functional prototypes and end-use products that must withstand harsh environments.
Cobalt
Cobalt is a high-strength metal used in SLM for creating parts that require excellent wear resistance and thermal stability. It is particularly valuable in the production of components for the aerospace, medical, and industrial sectors, where durability and performance under extreme conditions are essential. Cobalt parts produced with SLM exhibit fine detail resolution and robust mechanical properties, making them ideal for demanding applications such as turbine blades, cutting tools, and dental implants.
Nickel
Nickel is a versatile and corrosion-resistant metal used in SLM 3D printing for producing parts that require durability and high thermal and electrical conductivity. It is commonly used in applications such as chemical processing equipment, electronic components, and aerospace parts, where performance in harsh environments is critical. Nickel parts created with SLM offer excellent mechanical properties and can be used in a wide range of industrial and engineering applications, thanks to their strength and resistance to oxidation.
Precious Metals
Precious metals like gold, silver, and platinum are used in SLM for creating high-value parts that require exceptional ductility, conductivity, and aesthetic appeal. These metals are ideal for producing jewelry, medical devices, and electronic components where both functionality and appearance are important. Parts made from precious metals using SLM exhibit excellent detail resolution, surface quality, and mechanical properties, allowing for the creation of intricate and valuable items that meet both performance and aesthetic requirements